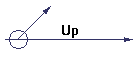
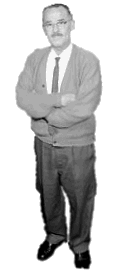
Stan Thompson
| |
[ Uranium Fuel ] [ Breeding Pile ] [ Bad Shit ] [ SGT's Facilities ] [ SGT's Process ] [ Michele Gerber ]
Thompson's Process
From: PLUTONIUM PRODUCTION STORY AT THE HANFORD SITE:
PROCESSES AND FACILITIES HISTORY (Document Number WHC-MR-0521
)
by Michele Gerber, Ph.D. and is
available to download.
4.1.10
The Bismuth-Phosphate Process
The bismuth phosphate essentially dissolved the jackets off of irradiated
U fuel elements, then dissolved the fuel itself, and then carried out a series
of precipitations followed by centrifugation and re-dissolving of the
precipitate cake. The valent state
of the Pu-239 (known as "product" at this stage) was manipulated so
that it would stay with, or separate from, the various solutions and precipitate
cakes produced in the operations. In
the +4 (tetravalent) state, the Pu-239 would carry with the bismuth
phosphate-based solutions. In the
+6 valent state (hexavalent), the Pu-239 would not carry with the bismuth
phosphate, and a by-product precipitation could be achieved.
The plutonium was reduced (taken to the tetravalent state) by adding
oxalic acid or ferrous ions, and oxidized (taken to the hexavalent state) by
adding sodium bismuthate (when bismuth phosphate was the carrier), or potassium
permanganate (when lanthanum fluoride was the carrier).
Actually, lanthanum fluoride was known to be a better carrier of
plutonium, in that it could carry with a smaller bulk or volume and could carry
away the stronger lanthanides such as Cs, Sr and La.
However, it was/is very corrosive, and for
that reason it was rejected for the main phase of the Hanford separations
process.
4.1.11
Dissolving
The first step in the separations process carried out at HEW was
dissolving, a process that removed the aluminum fuel jackets from the uranium
elements. It was carried out in the
dissolvers and metal solution storage tanks located in Sections 3 and 4 (Cells
5, 6 and 7) of the canyon buildings (T- and B-Plants).
The irradiated, jacketed fuel rods first were placed in boiling sodium
hydroxide, to which sodium nitrate slowly was added (reduce the formation of
hydrogen). This step produced
"coating removal waste." Next,
three metric tons of declad metal were charged into a dissolver.
Nitric acid was added in three increments, enough to dissolve one ton in
each increment. In order to keep
the time cycle as short as possible, "a substantial metal heel" was
left
[xc]
in the dissolver between charges. New
material was charged on top of this heel.
4.1.12
Extraction
The second step in the process was the extraction step.
This operation separated the product (Pu-239) from most of the uranium.
It also removed about 90% of the fission products into what was called
the metal waste solution. The
extraction step reduced the gamma radiation activity level by a factor of 10.
In the first extraction step, plutonium was kept in the +4 (reduced)
valent state. Bismuth nitrate and
phosphoric acid were added to the solution that contained the dissolved fuel
elements, causing the formation of bismuth phosphate.
A product precipitation (one that carried the Pu with it) then occurred.
The precipitate was centrifuged to separate the solid portion from the
liquid. The liquid portion was
jetted away as waste. The solid
portion ("precipitate cake"), which contained the Pu, was placed in
another tank and dissolved with nitric acid.
Sodium bismuthate or potassium permanganate were added to the
plutonium-bearing solution to oxidize the Pu to the +6 state, and then sodium
dichromate was added as a holding agent to keep the Pu steadily fixed in this
state. The BiPO4 then precipitated
as a byproduct, leaving the Pu in solution.
4.1.13
Decontamination
The third step, decontamination, essentially was a repetition of the
extraction process. The
final decontamination cycle reduced the gamma activity level by a factor of
10,000, giving an overall process "decontamination factor" of 100,000
below that of the original uranium solution.
The plutonium-bearing solution from the extraction step was reduced with
the addition of ferrous ammonium sulfate. Then,
bismuth nitrate and phosphoric acid again were added, a product precipitation
occurred, and the precipitate was centrifuged.
The solid portion, containing the Pu, was liquified with nitric acid,
oxidized, and the remaining BiPO4 precipitated away as waste.[xci]
4.1.14
224 Bulk Reduction Process
Plutonium-bearing solution was transferred from the "tail" ends
of the canyon buildings to the 224 Buildings via underground piping.
The starting batch size in the latter facility was 330 gallons.
Here, the Pu solution from the 221 buildings was oxidized with sodium
bismuthate. Phosphoric acid then
was added to produce a byproduct precipitation, leaving the Pu in solution.
Centrifuging then separated the solution and precipitate.
Nitric acid was added to dissolve the byproduct cake, and it became
waste. Next, the plutonium-bearing
solution was oxidized with potassium permanganate (KMnO4).
Hydrogen fluoride and lanthanum salts were added, in what was known as
the "crossover" step. A
lanthanum fluoride precipitate was produced, leaving hexavalent Pu in solution.
Impurities were precipitated in a byproduct
cake, as the fission products were carried with the lanthanum.
This byproduct cake contained all of the lanthanides (cerium, strontium,
lanthanum, etc.) that the BiPO4 could not carry out of the stream.
The cake was dissolved in nitric acid, neutralized with sodium hydroxide,
and sent to tanks for settling. The
plutonium solution then was reduced to +4 state by adding oxalic acid.
Lanthanum salts and hydrogen fluoride again were added, thus
precipitating lanthanum fluoride that contained the Pu.
The precipitate was separated by centrifugation, and potassium hydroxide
was added to metathesize the Pu lanthanum fluoride, forming a solid Pu lanthanum
oxide. (Metathesis is a chemical
process to convert a solid to another solid.)
Any liquid was removed by centrifugation, and the solid Pu lanthanum
oxide was then dissolved in nitric acid to form Pu nitrate.
By this time, the original 330-gallon batch that had entered the 224‑T Building
had been concentrated to eight gallons (volume).[xcii]
4.1.15
231 Isolation Process
Lastly, the plutonium nitrate from the 224 facilities was sent to the
231-Z Building for the final processing that could be done at the Hanford
Engineer Works. Hydrogen peroxide,
sulfates, and ammonium nitrate were added to the plutonium-bearing solution.
The hexavalent Pu precipitated as plutonium peroxide.
Nitric acid then was added to dissolve this precipitate.
The Pu nitrate then was placed in small shipping cans and boiled right in
these cans, using hot air. It was
reduced to a wet nitrate paste. In
this form, the Pu was stored in the 213-J and K vaults in the southeast end of
Gable Mountain, and then shipped to the secret Los Alamos Site.
Each shipping can held about one kilogram (kg) of Pu.[xciii]
4.1.16
Earliest Operations
Operating experiences during the initial months of canyon operations were
described by DuPont as unusually satisfactory."[xciv]
No serious mechanical problems developed, except that the bowl of the
centrifuge in Section 16 of T-Plant jammed against some dip tubes when it was
run backwards on January 5, 1945. The
centrifuge was replaced via remote operations, partially decontaminated in a
spare cell, and then buried in 1954 when it was determined that it could not be
repaired. This and other
miscellaneous remote tasks gave operators confidence that "the Canyon
Buildings can be operated remotely as planned and with somewhat less loss of
fabricated equipment than originally anticipated."[xcv]
During the next six months of canyon operations, procedures were
standardized. Technical efforts
were directed towards reduced time cycles, as production sped for the special
nuclear materials needed to win the war. By
mid-1945, emphasis had shifted to "a review of process technology and
operating technique in an effort to improve efficiency and reduce waste
losses."[xcvi]
Free nitric acid concentration was reduced to obtain an increase in the
specific gravity of dissolver solutions. The
most significant improvement, however, came in the late summer, with the
installation of piping to allow for intermediate solution transfer from storage
to the precipitators in Section 6 (Cells 11 and 12).
This was a safety measure, as metal solution slightly in excess of charge
requirements then could be taken from storage, agitated, and sampled so that the
correct amount, based on critical mass limitations, could be transferred to the
extraction sections of the plant. Further
safety improvements included more rigorous efforts to empty and decontaminate
the precipitators used in the extraction and decontamination cycles.
These measures assured the prevention of Pu-239 buildup on equipment.
4.1.17
Early Process Changes
The original HEW separations canyons were designed on the basis that one
plant would have the capacity to process the output from one pile (reactor).
With each HEW reactor originally planned to produce one metric ton of
metal (containing approximately 250 grams of product - Pu-239) per day, the
earliest standard procedure for T-Plant involved starting a one metric-ton
charge of metal into the dissolvers about every 26 hours.
However, by the summer of 1945, production tests had shown that charge
size could safely be increased to 1.5 metric-tons of metal, "without
noticeable effect of yield or equipment performance."[xcvii]
By September 1, process modifications enabled the plant to complete the
processing of a charge in just 20 hours, with only a 10% allowance added onto
the average process cycle for equipment repairs.
Other very early changes included the elimination of potassium carbonate
from the separations process in February 1945, and one month later, due to the
unavailability of potassium hydroxide containing only 0.0005% iron impurity, the
relaxation of process specifications for this chemical to allow for 0.005% iron
impurity. Overall, the first
full-scale separations experiences at T-Plant and at the 224-T Bulk Reduction
Building and the 231-Z Isolation Building, led to large reductions in many
essential materials, per unit of production.
For example, the strength of the key dissolving agent nitric acid was
decreased from an average of 95% to an average of 69% (a 33% reduction).
By September 1, 1945, other chemical requirements were reduced by an
average of 41%, and potassium carbonate had been eliminated from the process
altogether.
Additional and ongoing process improvement studies carried out during the
1945-46 period were directed at: simplification
of operations to achieve reductions in process time, modification of the process
to increase canyon capacity per batch, reduction in waste volumes, recovery of
additional product from wastes, the establishment of better understandings of
process safety and safety limits,
[lxxxv].
DuPont, IN-6263.
[lxxxvi].
DuPont, Construction, HAN-10970, Vol. III, pp. 861-919.
[lxxxvii].
DuPont, Construction, HAN-10970, Vol. III, pp. 905-908;
Gerber, WHC‑MR‑0452.
[lxxxviii].
DuPont, Construction, HAN-10970, Vol. III, pp. 913-915;
Gerber, WHC‑MR‑0452.
[lxxxix].
DuPont, Construction, HAN-10970, Vol. III, pp. 917-919;
Gerber, WHC‑MR‑0452.
[xci].
Hanford Engineer Works, HW-10475-C; Stoller and Richards, Reactor
Handbook, 2nd ed. pp. 227-234.
[xcii].
Hanford Engineer Works, HW-10475-C.
[xciii].
Hanford Engineer Works, HW-10475, Section C; Swartout, HW-3-2801.
[xciv].
DuPont, Operation, HAN-73214, Book 12, p. 75.
[xcv].
DuPont, Operation, HAN-73214, Book 12, p. 76; G.E. Hanford
Co., "Property Disposal Report," #54-217, May 23, 1954.
[xcvi].
DuPont, Operation, HAN-73214, Book 12, p. 145.
[xcvii].
DuPont, Operation, HAN-73214, Book 12, p. 49.
|