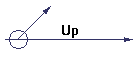
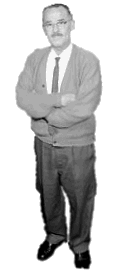
Stan Thompson
| |
[ Uranium Fuel ] [ Breeding Pile ] [ Bad Shit ] [ SGT's Facilities ] [ SGT's Process ] [ Michele Gerber ]
Breeding in the Reactors
From: PLUTONIUM PRODUCTION STORY AT THE HANFORD SITE:
PROCESSES AND FACILITIES HISTORY (Document Number WHC-MR-0521
)
by Michele Gerber, Ph.D. and is
available to download.
2.0
IRRADIATION PROCESSING AT THE HANFORD SITE
2.1
HANFORD'S SINGLE PASS REACTORS
Nine plutonium production reactors, now closed and silent, cluster along
a 14-mile (22.53 kilometers) stretch of the Hanford shoreline of the
Columbia River. Eight of these
reactors, all except the N Reactor, are known as "single-pass"
reactors due to the once-through nature of their light water cooling systems.
Known as "piles" in the 1940s, these machines drew cooling
water from the river, and pumped it through a series of filtration, chemical
treatment, and storage buildings and tanks.
The water then was passed directly through long, horizontal tubes in the
reactors, where the solid, Al-Si-jacketed uranium fuel rods underwent active
neutron bombardment. From there,
the water was pumped out the back of the piles, left for a brief time (30
minutes to 6 hours) in retention basins to allow for short-term radioactive
decay, and then returned to the Columbia River.[xxii]
2.1.1
Historic Significance of B-Reactor
Hanford's original reactor, B, was the first such full-scale nuclear
facility to operate in world history. Built
by the Army Corps of Engineers and the DuPont Corporation in just 11 months
between October 1943 and September 1944, it now is listed on the National
Register of Historic Places. B
Reactor also has received special awards from the American Society of Mechanical
Engineers and the American Society of Civil Engineers.
2.1.2
Single-Pass Reactor Buildings
The next seven reactors, D, F, H, DR, C, KE, and KW (in order of
construction) were similar in most features.
Built between 1943 and 1955, and shut down between 1964 and 1971, they
had an average life span of just 21 years.
The construction and general specifications of B, D and F Piles (the
original three reactors built in World War II) were similar to those of most of
Hanford's other single-pass reactors, although C, KE and KW were slightly larger
and contained some special features. All
of the piles rested on thick concrete foundations topped with cast iron blocks.
The reactor buildings themselves were reinforced concrete structures
shaped like tiered wedding cakes with no containment domes.
They sat near the centers of five separate reactor areas of approximately
700 acres (283.28 ha) each.
The core of each reactor was a series of graphite blocks that fitted
together. In the oldest
six reactors, the cores each measured 28 feet (8.53 meters) from
front to rear, 36 feet (10.97 meters) from side to side, and
36 feet (10.97 meters) from top to bottom.
In the K-Reactors, the cores each were 33 feet (10.06 meters) from
front to rear, 40 feet from side to side, and 40 feet (12.19 meters) from
top to bottom. The graphite served
as the "moderator" to slow and absorb extraneous neutrons from the
basic nuclear chain reaction. Each
stack was pierced front to rear by aluminum process channels that held the fuel
elements. The first six Hanford
reactors each contained 2,004 process channels, and the KE and KW Reactors each
contained 3,220. The
"lattice," or pattern of process channel configuration was a simple
rectangle, with only the corners of the core bearing no penetrations. Each
reactor's graphite core was surrounded by thick thermal and biological shields.
The core and shields formed the reactor "block," and each block
was enclosed in a welded steel box that functioned to confine a gas atmosphere.
The atmosphere of the earliest reactors was composed of helium, an inert
gas selected for its high heat removal capacity.[xxiii]
At the front and rear of each process channel, a carbon steel exit and
entry sleeve known as a "gunbarrel" penetrated the pile shields.
The ends of each process tube flared into flanges to facilitate a close
fit and interface against the gunbarrels. Asbestos
gaskets lay between the flanges and the stainless steel nozzles that projected
from the front and rear of each process tube.
The nozzles connected to coiled lengths of aluminum tubing known as
"pigtails" (originally one-half inch (1.27 centimeters) in
diameter but later larger), which in turn connected to stainless steel
crossheaders. Devices known as
"Parker fittings"
connected the pigtails to the crossheaders.
The crossheaders [originally 39 sections of four-inch- (10.16‑centimeter‑)
diameter pipes] served to break down the huge water supply entering the reactor
building's valve pit via two 36-inch- (91.44‑centimeters‑) diameter
headers, then two 36-inch (91.44 centimeters) risers.[xxiv]
Test holes extended from the right side of each Hanford pile for the
irradiation of experiments and special samples.
Horizontal channels for control rods (HCRs) entered from the left side of
each reactor, and vertical channels for safety rods (VSRs) entered from the top.
The control and safety systems functioned simply to absorb neutrons, thus
slowing and eventually stopping the controlled chain reaction of neutron
exchange between the uranium fuel elements.
The early Hanford reactors also were equipped with various safety and
control instruments that measured temperature, pressure, moisture, neutron flux
and (radio)activity levels in the byproducts of the fission reaction.
Because no one instrument had enough range to measure neutron flux all
the way from shutdown (background) levels to the approximately 1,000,000,000,000
(1 trillion) times background levels experienced during operations, each reactor
was fitted with sub-critical, mid-range and full power flux instrumentation.[xxv]
2.1.3
Operation of the Single-Pass Reactors
During actual operations, raw water was pumped from the Columbia River by
pumphouses (known as 181 Buildings) located at and partially in the river.
From there, water for the earliest reactors was pumped to the 182
Buildings, which routed much of the water to the 183 Buildings for chemical
treatment, settling, flocculation and filtration.
A small portion of the water proceeded directly from the 182 Buildings
through large concrete pipes to the Hanford's 200 Areas [located 6 to 8 miles
(9.66 to 12.87 kilometers) away] for treatment and use there in chemical
separations and other operations. From
the 183 Buildings, Hanford's reactor process water was pumped to the 190
Buildings and stored in huge "clearwells" ready for pile use.
In the 190 buildings, sodium dichromate was added to the water to prevent
corrosion of pile process tubes. The
190 Buildings then supplied the reactors themselves as needed.
Some of the earliest HEW reactor influent systems also contained 185
Buildings for dearation, and 186 Buildings for refrigeration of coolant water.
However, these functions were found to be unnecessary and the 185 and 186
Buildings were diverted to other uses.
At HEW's earliest reactors, each process tube usually was charged with 32
U fuel elements, along with a few dummy slugs in various configurations (either
solid or perforated and hollow) at each end of the process channel.
Many fuel configurations could be used to achieve various desired flux
patterns across the reactor lattice.
2.1.4
Change and Experimentation in Production Process
The history of Hanford's single-pass reactor operations is one of
constant change and experimentation. Many
questions puzzled and intrigued early Hanford scientists.
For example, they worried about the possibility of "slug
failures," or the accidental penetration by cooling water of the aluminum
jackets surrounding the fuel elements. They
knew that such penetration would cause the uranium to swell, thus blocking the
coolant flow within the process tube. This
condition would necessitate tube removal and replacement, and could melt the
fuel elements in that tube. Also,
fuel ruptures would allow the escape of radioactive fission products in larger
than average amounts.[xxvi]
Another topic that intrigued the early operators of Hanford's reactors
was that of temperature and neutron flux distribution.
At first, "poisons" (neutron absorbing materials) were
distributed in a uniform pattern throughout the reactor core during operation.
This method of control produced a flux pattern that resembled a cosine
(or bell) curve, front to rear within the pile.
Such a curve meant that while uranium elements in the center of the
reactor achieved maximum or optimum irradiation, many of the fuel elements
located in the rest of the reactor achieved sub-optimal irradiation, due to
lower neutron flux. This situation
not only was inefficient in terms of utilization of the uranium supply, it also
contributed to temperature gradients that caused expansion in the graphite in
the central portions of the pile.
Shortly after World War II, Hanford scientists tested several new poison
patterns, with the goal of "flattening" the pronounced cosine curve,
thus evening out the distribution of neutron activity and enlarging the area of
maximum flux and temperature within the reactor.
Quickly, they learned that many alterations in poison distribution
(control rod positions) would achieve higher and lower temperatures and
exposures in various reactor zones. They
dubbed all of these manipulations "dimpling" the reactor.[xxvii]
2.1.5
Graphite Expansion Early Problem
Of all the operational questions and issues that were pioneered in the
Hanford reactors, almost none proved more compelling than those involving the
graphite. Swelling (expansion) of
the graphite, along with embrittlement, was a side-effect of irradiation.
By late 1945, graphite expansion was causing the process tubes to bow,
"binding" them too tightly with their fittings and other components,
and straining the seals at the top and side corners of the reactor shields.
As a result, a Graphite Expansion Committee was formed at Hanford in
early 1946.[xxviii]
Ultimately, concern over the graphite expansion problem and its intrinsic
threat to pile "life" led to the decision on March 15, 1946, to shut
down B Reactor.[xxix]
However, in mid-1947, convinced by positive developments in graphite
study, site managers made the decision to restart the reactor the following
year.[xxx]
By 1950, further experiments had made it clear that the addition of
carbon dioxide (CO2) to the helium in reactor gas atmospheres could
alleviate much of the graphite swelling problem.
The CO2, because it had a lower heat removal capacity than the
helium, allowed the carbon atoms in the graphite crystal, displaced by
irradiation, to heat up, become active, and hence realign themselves.
By 1954, the CO2 additions were working so well the oldest
reactors operated with a gas atmosphere composed of 40% helium and 60% CO2,
and tests were being planned to try even higher proportions of CO2.[xxxi]
2.1.6
Increased Power Levels/Production
Beyond even the graphite puzzle however, no early (and ongoing)
operational issue was more important to the Hanford Works than that of
increasing the power levels. B Reactor,
along with D, F, and DR, was designed to operate at 250 megawatts (MW -
thermal), while H, built five years later, was designed for 400 MW.
C Reactor, built during 1951-52, was designed for 650 MW, but the
learning curve in pile operations took such a leap that the twin K Reactors (KE
and KW) were built during 1953-55 designed for 1,800 MW each.[xxxii]
Questions concerning how to achieve higher power levels, with consequent
increases in plutonium production, had intrigued Hanford scientists since World
War II. In April 1949, an
incremental test program that would take D‑Reactor to 330 MW was
undertaken. By January 1950, this
experiment was so successful that DR-Reactor was being operated at 400 MW.[xxxiii]
With the acceleration of the Cold War, increased power levels in the
Hanford reactors became even more important to perceived national defense needs.
From the late 1940s through the closure of the last single-pass reactor
in 1971, pile history at Hanford was dominated by constant efforts to achieve
increased power levels.
By late 1956, under President Eisenhower's policy of "massive
retaliation" and the boisterous challenges of Soviet Premier Kruschchev,
the World War II power levels at the three oldest reactors had more than
tripled, and stood at 800 MW. At
that time, a thorough set of modifications designed to allow increased coolant
flow was completed at these reactors. Similar
modifications were made at the other single-pass reactors through the early
1960s, spurred by the threat of Soviet technical superiority as demonstrated by
Sputnik. As a result of these
changes, and of fuel and tube design improvements, power level increases in the
World War II reactors reached the 2,200 - 2,400 MW range by the mid-1960s, just
after the Cuban "missile crisis" had once again boosted American
desired for a strong nuclear defense. The
mid-1960s operating figures in the HW reactors were nearly 10 times the original
design levels. At the KE and KW
Reactors, final operating levels in 1970 and 1971 stood at approximately 4,100
MW each.[xxxiv]
Higher power levels themselves were easy to achieve, simply by adding
enriched uranium fuel elements (those containing higher percentages of U-235).
However, increased power levels presented many puzzling operational
challenges in the effects they imposed on reactor systems and components.[xxxv]
By mid-1951, Hanford scientists knew that the higher temperatures
associated with increased power levels could produce substantially higher fuel
jacketing and tube corrosion rates (and failure rates).[xxxvi]
However, their main concerns centered around how to deliver additional
cooling water to, through, and out of the reactors.
Such water would be needed to offset "boiling disease," the
Hanford term for a situation wherein steam might form in a process tube.
If this happened at higher power levels, greater water pressures would be
needed to sweep the steam from the tube (and thus to prevent a localized
meltdown).[xxxvii]
2.1.7
Operating Challenges at Higher Power Levels
By mid-1953, effluent removal piping at the oldest reactors, already
operating at 20% to 50% above design capacity, was under intense
study.[xxxviii]
At the same time, operators realized that the filtration capacity for
intake water would have to be increased well beyond the original capacity of
approximately 35,000 gallons (132 489.42 liters) per minute (gpm) per
reactor. More important, however,
was the need to increase the intake pumping capacity.[xxxix]
In the meantime, as power levels crept upward in the oldest reactors
during the late 1940's and early 1950's, fuel element ruptures became a reality.
The first rupture occurred at F Reactor in May 1948, and two others
occurred later that year at B Reactor.[xl]
The number of fuel element rupture incidents increased slowly during
1949-1950, but expanded dramatically in 1951 when Hanford Works experienced 115
fuel failures.[xli]
This number continued to climb throughout the early 1950s, bringing
further focus to fuel fabrication improvement studies.
Along with fuel element failures, higher power levels and higher
temperatures brought increasing levels of corrosion and failure of process
tubes. By 1953, each Hanford
reactor needed an average of 200 tube replacements per year.[xlii]
In order to reduce the ruinous corrosion, a special "Flow
Laboratory" was built in late 1951 in a modified WWII refrigeration
building. It functioned to study
corrosion and heat transfer within process tube "mock-ups" (simulations).[xliii]
At the same time, the Hanford Works began an intense review of intake
water treatments.[xliv]
Sodium dichromate, a key corrosion inhibitor that had been added to
reactor water since World War II, was evaluated closely.
Because sodium dichromate was known to have detrimental effects on the
fish of the Columbia River, much experimentation with other corrosion blockers
was undertaken.[xlv]
However, due to dramatic rises in tube and fuel element corrosion when
the sodium dichromate was withdrawn, site scientists decided to continue using
it.[xlvi]
The drive to higher and higher power levels in Hanford's reactors
throughout the late 1940's and mid-1950's was accompanied by the need for
several changes to enhance operating safety.
The "last ditch" safety system in the five oldest reactors was
replaced with tiny, neutron-absorbing, nickel-plated carbon steel balls.
These balls were poised in hoppers at the top of the piles, ready to pour
in and tamp down the fission reaction if necessary.[xlvii]
Physical braces and supports, and many additional instruments also were
added.[xlviii]
Other changes in reactor operations shortened the time required to
perform routine operating chores. Since
World War II, charge-discharge ("C-D") operations (loading and
unloading the fuel elements from a reactor) were performed while a reactor was
shut down. However, by 1950
experiments were underway to perform C-D operations while a reactor was running.[xlix]
During the early and mid-1950s, such a system was tested successfully.
It operated remotely, and worked by flushing fuel elements down the
process tubes via high pressure water.[l]
Due to cost, this system were not installed at the oldest five reactors,
but it was emplaced in the other, newer reactors.
Another change aimed at saving shutdown time in the Hanford reactors
concerned "purging" or cleansing the process tubes.
Minerals, elements and suspended solids in the Columbia River's water
routinely built up a film on the process tube surfaces.
This situation caused heat build-up within the reactors.[li]
Since World War II, operators had "purged" (scrubbed) the film
from the tubes on a monthly basis, while the reactors were shut down.[lii]
However, by the early 1950's the Hanford Works was trying to conduct
"hot" purges -- so called because they occurred while the reactors
were running. Such operations were
very effective in removing reactor films, but greatly increased the levels of
pollution entering the Columbia River.[liii]
To help ameliorate the high levels of radioactivity, restrictions were
placed on the frequency of purges that could be conducted during autumn periods
of low river flow. Also, a series
of experiments was initiated to find ways to protect the river.[liv]
2.1.8
Reactor Upgrades for Increased Production
Beginning in 1954 and continuing into the early 1960s, a series of major
modification projects designed to strengthen the reactor systems necessary to
support power level increases were emplaced at the eight single-pass Hanford
piles. Designated "Reactor
Plant Modifications for Increased Production," these projects substantially
increased intake pumping, filtration, and chemical treatment and storage
capacities.[lv]
Effluent systems likewise were strengthened and enlarged dramatically.[lvi]
Instrumentation with higher range capacity was emplaced.[lvii]
Electrical upgrades and many other miscellaneous changes were made within
reactor systems. One such
modification was the removal of aluminum liners (known as "thimbles"
by Hanford workers) in some of the process channels, because higher operating
temperatures would cause these liners to melt.[lviii]
Ironically, just as these projects were underway, significant changes in
fuel elements and process tube designs and materials took place at the Hanford
Works. These developments allowed
dramatic increases in reactor power levels, once again straining the newly
upgraded support systems. Much of
the increase in power level was made possible by the use of the I&E fuel
elements, which were first tested on a production basis in 1958.[lix]
Other operating efficiencies that came quickly in the late 1950's and
early 1960's resulted from the gradual replacement of aluminum process tubes
with tubes made of Zircaloy-2. Also,
self-supported (projection, bumper or ribbed) fuel elements were developed at
Hanford. Such fuel elements allowed
greater passage of cooling water, again allowing higher power levels to be
sought within a margin of safety.[lx]
2.1.8.1
Maintenance and Safety Issues at Single-Pass Reactors.
The higher power levels permitted by the development of internally and
externally cooled fuel elements, ribbed fuel elements, and new process tubes,
brought multiple operating challenges to the support systems of the Hanford
reactors. Pumps and pipes developed
destabilizing leaks, while electrical capacities proved inadequate.
Much of the reactor instrumentation also was rendered obsolete.
Even the graphite swelling problem increased, as the levels of neutron
flux and bombardment rose exponentially.[lxi]
Safety reviews called for a mounting list of improvement projects.[lxii]
From that time forward, the story of the Hanford single-pass reactors
became one of how to design and fund all of the support systems upgrades that
were needed. One project that was
accomplished at all of these reactors during 1960-62 was the construction of a
large exhaust gas confinement system. It
was comprised of a below-ground filter building, duct work that routed gases
from the reactor through these filters and then back into the exhaust stack, and
sampling equipment. Another part of
this project provided a rear face fog spray system for each reactor, and a front
face fog spray system at C, KE and KW Reactors.[lxiii]
Additionally, the Ball-3X systems at most of the reactors were upgraded
in the early 1960s, as part of an overall "exposure reduction program"
undertaken by Hanford's Irradiation Processing Department.[lxiv]
Several instrumentation improvements and replacements also were approved
for many of the reactors, based on safety and control considerations.[lxv]
2.1.9
End of Single-Pass Operations
In January 1964, President Lyndon Johnson announced that, due to a
decreased need for special nuclear material (SNM), Hanford's reactors would be
shut down in a phased sequence beginning in December 1964.[lxvi]
At the same time, Columbia River pollution from reactor effluent was
becoming an increasingly important factor in regional and national
considerations. Hanford scientists,
as well as health officials in Washington, Oregon and the U.S. Public Health
Service became more and more concerned with the effects of reactor effluent in
the huge river. By 1960, the total
volume flow from the Hanford reactors had increased approximately ten-fold over
that of the World War II period, shortening the practical retention time to
only about 30 minutes and making diversion of unusual effluents to
"cribs" (percolating areas dug into the earth) or other holding areas
virtually impossible. Furthermore,
the total amount of radioactivity reaching the Columbia River stood at nearly
14,000 curies per day.[lxvii]
Within this effluent flow, the main isotopes of concern were phosphorus
32 (P-32), zinc 65 (Zn-65), chromium 51 (Cr-51), iron 59 (Fe-59), and arsenic 76
(As-76). It had been known since
the late 1940s that these isotopes concentrated
within aquatic plants and animals to vastly higher levels than were found in the
river water itself. Multiple
studies pointed to the fact that the Columbia's water could be at or below
permissible levels for various radionuclides, and still present a hazard to
consumers of river fish, ducks and other wildlife.[lxviii]
Throughout the late 1950s and early 1960s, virtually every aspect of the
bioaquatic and potential downstream health consequences of reactor effluent was
examined, including the effects of temperature, operating purges, various purge
agents and filtration aids, fuel element ruptures, sodium dichromate, and the
radionuclides themselves.[lxix]
Various solutions were proposed and tested.
Salient among these was the concept of passing reactor effluent through
beds of aluminum shavings, in order to entrap various radionuclides.[lxx]
Laboratory tests seemed promising, but a production-size bed installed in
1960 at the D Reactor retention basin demonstrated so many shortcomings that the
idea of decontamination of reactor effluent via aluminum test beds was
effectively abandoned in 1961.[lxxi]
Another concept that was explored thoroughly at Hanford was that of
varying the intake water treatments. However,
mixed results, combined with undesirable side effects, resulted in very little
practical improvements.[lxxii]
In the early 1960s, an idea that had been explored in the 1950s for
reducing radionuclide releases to the Columbia River was revived.
This "Inland Lake" concept proposed routing reactor effluent
through trenches to artificial, inland lakes dug in the center of the site where
the distance between land surface and the underground water table was
significantly greater than it was near the reactor retention basins.
Proponents of the idea pointed to the longer time period for radioactive
decay and thermal cooling of effluent, before the wastes finally would reach the
river. However, studies conducted
in the 1950s had demonstrated undesirable effects, including the wind
entrainment of radioactive mists that could spread contamination over wide areas
extending even to offsite. Furthermore,
problematic underground mounds in the water table, caused by disposal of
low-level liquids wastes from chemical processing plants near the center of the
site would be worsened by the addition of reactor effluent.[lxxiii]
As the reactor shutdowns began at Hanford in the mid-1960's, operators
and scientists struggled to extend the viability of the remaining piles by
developing environmentally acceptable means of effluent disposal.
In the spring of 1967, with five single-pass reactors operating, a
Hanford summary report on alternate methods of reactor effluent treatment and
disposal listed several additional options.
Conversion to recirculating cooling systems was listed as economically
prohibitive, since it would involve providing 400,000 gallons (1 514
164.75 liters) per minute of additional cooling (pumping) capacity per
reactor, with all attendant piping modifications.
Other related equipment also would be needed for each reactor, for a
total conversion cost of $32 million per reactor.
Other potential solutions also were expensive and posed awkward siting
problems between the reactors and the Columbia River.
Still other, less expensive proposals each came with physical or
acceptability barriers.[lxxiv]
The eight single pass reactors at the Hanford Site all closed permanently
between December 1964 and January 1971.
2.2
N REACTOR OPERATIONS
The Hanford Site's ninth defense production facility, N Reactor, operated
from early 1964 to December 1986. Like
Hanford's single-pass reactors, N Reactor was tied in umbilical fashion to the
Columbia River, and it was light water cooled, graphite moderated, and fueled
with bored metal uranium. Also,
none of the defense production reactors at the Hanford Site were equipped with
containment domes. Nevertheless,
there were major differences between N Reactor and the older Hanford piles.
N Reactor recirculated its primary coolant water, instead of returning it
to the river, thus releasing significantly less radioactive effluent (waste
water) on an everyday basis. Additionally,
the light water coolant circulated under pressure, allowing for much higher
operating temperatures, and the water was demineralized so that less film was
deposited inside the process channels.
Another major difference between N Reactor and the older Hanford piles
was that N Reactor had a negative-void coefficient design, while the single
pass reactors had a positive-void coefficient design.
The negative-void factor was a crucial safety feature because it meant
that when a steam bubble or void developed in a process tube, the effect tended
to shut down N Reactor. This factor
prevailed because, at N Reactor, there was a low ratio of graphite moderator to
U fuel. The cooling water provided
a significant portion of the moderating effect.
Thus, loss of coolant had the effect of reducing reactivity.
In the single pass reactors, a steam bubble or void tended to increases
the neutron flux logarithmically, thus enhancing the chances for a nuclear
accident. Lastly, in 1966, the
steam generated from the heat of the nuclear chain reaction was captured at N
Reactor to produce electricity for the domestic power needs of the Pacific
Northwest. Today, N Reactor
remains as the only U.S. defense reactor that served a "dual purpose."[lxxv]
2.2.1
105 N Building and Reactor
The 105-N (N Reactor) Building was a reinforced concrete structure
sitting atop a thick slab of reinforced concrete.
The reactor core itself was 39 feet (11.89 meters), 5 inches
(12.70 centimeters) high, 33 feet (10.06 meters) wide, and 33
feet (10.06 meters), 4.5 inches (11.43 centimeters) tall.
It consisted of 1,800 tons of nuclear grade graphite blocks notched,
interlaid and pierced by 1.004 process channels.
The lattice was arranged in a rectangle 32 feet (9.75 meters) high
by 34 feet (10.36 meters) wide, with 21 channels omitted from each corner.
Eighty seven HCRs entered the N Reactor core, 41 from the left side
and 46 from the right side. One
hundred and eight vertical safety channels existed to receive ceramic
"3X" balls to shut down the reactor in case of need.
A small number of other channels pierced the core to hold experiments,
and to position traverses to measure graphite distortion over time, graphite
temperature, and flux. Graphite
bowing over time was both expected and feared by the designers of N Reactor.
The original reactor manual stated that "there is as yet no
determination of the maximum extent to which contraction of nuclear graphite can
be induced by irradiation." An
8.3-inch (21.08 centimeters) depression at the top center of the graphite
moderator was chosen as the original design basis, corresponding to about a
three percent contraction, while 12 inches (30.48 centimeters) was
"estimated to be tolerable for the reactor as built."
The design lifetime of the reactor was 25 years.[lxxvi]
The N Reactor core was surrounded special layers of reflector graphite,
then by water cooled thermal shields constructed of boron steel and cast iron,
and then surrounded again by a primary shield of high density concrete.
Helium gas formed the pile atmosphere.
A fog spray system at both the front and rear reactor faces was provided
for contamination control and cooling in case of a loss of contaminated steam
from the core. The water influent
system began at the 181-N River Pump House, proceeded to the 182‑N High
Lift Pump House where raw river water was treated and where demineralized and
deoxygenated water was injected into the makeup and cooling water, the 183‑N flocculation
and filter plant, and to the 183-NA Pump House that sent coolant water into the
reactor. Extra supplies of treated
water were held in the 183-NB clearwell. N
Reactor's primary coolant system used from 100 to 1,500 gallons (378.54 to
5 678.12 liters) per minute of fresh, treated water, a vast decrease
from the 35,000 to 105,000 gallons (132 489.42 to 397 468.25 liters)
per minute consumed by Hanford's single pass reactors.[lxxvii]
2.2.2
N Reactor Operating Changes and Challenges
Over its years of operation, many changes took place at N Reactor.
From 1965-67, a "co‑product" demonstration campaign took
place, in which tritium was produced in the reactor from special lithium
aluminate fuel elements. Beginning
in 1966, N Reactor steam for electrical production was harnessed at the Hanford
Generation Plant (HGP) constructed just west of the pile by the Washington
Public Power Supply System (WPPSS). In
1971, N Reactor was ordered closed due to a diminished national need for defense
plutonium production. An agreement
was reached to keep the reactor running primarily for electrical production.
During the 1970s, a time when the entire Hanford Site undertook
modifications to achieve more desirable interfaces with the environment, a
number of upgrades to N Reactor's waste treatment systems were emplaced.
Trenches were dug to receive reactor effluent, thus allowing a longer
percolation time through the soils just inland from the reactor, for radioactive
decay to occur before effluents reached the Columbia River.
Monitoring instrumentation for waste products was added, secondary and
shield coolant loops were converted from single-pass to recirculating systems,
and a special containment tank was constructed to hold the pile purge effluent
for transfer to Hanford's high level waste storage tanks.
Release of this purge material to the Columbia River was discontinued.[lxxviii]
Beginning in the early 1980s, a large defense build-up was ordered by
President Ronald Reagan. At the
same time, N Reactor arrived at 20 years old and began to experience system
failures of many types. One
fundamental problem was the distortion of the graphite stack, where built-in
slip joints could not accommodate all of the local distortion, some block
cleavage, and actual separation of blocks that had occurred within the central
core. Such distortions produced
"significant changing problems" by 1982.
Additionally, the 1982 summer outage revealed center transverse
contraction resulting in a total sag of about three inches, and tube elongation
to the extent that many connector clearances were rated as "minimal."
As N Reactor struggled to remain a crucial piece of America's defense
arsenal, many system upgrades were undertaken.
In the 189/190‑D Thermal Hydraulics Laboratory, a complete
mock-up of N Reactor's core, in it's actual distorted and curved condition,
was built, in order to study remediation concepts.
An N Reactor Loop Components Test Facility, a high temperature,
pressurized, recirculating demineralized water test loop also was constructed to
model and evaluate leaks in the primary flush lines of the core, various valves,
and alternative ideas for operations. Another
model was built to test inspection and removal equipment for the graphite
cooling tubes, and to demonstrate a process tube drying system.
In April 1986, an accident at the Chernobyl nuclear plant in Soviet
Russia brought about a stand down for safety evaluations at N Reactor.
The reactor never re-opened. It
was ordered to cold standby by the DOE in February 1988, and a large D&D
project leading to final disposition began in 1994.[lxxix]
|